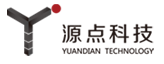
2024-07-01
Stretch film is an innovative plastic film made from Linear Low Density Polyethylene LLDPE, designed to wrap pallets and ensure load stability during transportation and storage. The ideal stretch film for your needs depends on your objectives, equipment, and the weight of the load you are securing. Additionally, stretch film is designed to use two main manufacturing methods: blown and cast.
Table of Contents
ToggleCast stretch wrap is produced through a cast extrusion process, which starts with a granular resin being fed into a heated screw barrel. At the same time, the molten resin is constantly fed through a narrow slot die. This method makes the chilled rollers rapidly cool and solidify the film instantly.
After that, tension rollers are started to draw the wrap to the winding and slitting stations. And the speed of the stretch film pulled determines the thickness and width. Compared with the blown extrusion method, cast stretch wrap is faster and saves labor and time.
The cast extrusion process offers several advantages:
Blown stretch wrap is produced using the blown film extrusion process. In this method, resin beads and additives are fed through a heated machine equipped with a circular die. The heated material forms a bubble, which is gradually cooled by air as it goes up the tower. At the top of the tower, the film is nipped together and then guided down to the winding and slitting stations with guide rollers. This process results in a tougher and more robust film with high puncture resistance.
Because of the complicated process and the lesser output per hour, the blown stretch wrap is more expensive than cast films. Hand stretch film is made with the process and typically owns superior strength and puncture resistance.
Different formulas and manufacturing processes result in various types of stretch films. Choosing the right stretch film depends on your specific requirements and needs. Here, we highlight the key differences between cast and blown stretch wrap.
Feature |
Cast Stretch Film |
Blown Stretch Film |
Clarity |
High clarity, ideal for showcasing products |
Hazy appearance, less clarity |
Appearance |
Very Clear & Glossy |
Hazy & Dull |
Noise Unwinding |
Quiet |
Noisier |
Production Speed |
Faster production speed, saving labor and time |
Slower production speed due to the complex process |
Strength |
Moderate strength, suitable for uniform loads |
Superior strength, ideal for heavy loads with sharp edges |
Puncture Resistance |
Moderate puncture resistance |
High puncture resistance |
Cling Level |
Consistent and high-level cling |
High cling, maintaining integrity during transportation |
Durability |
Good durability, tear-resistant |
Durability performs well in varying temperatures |
Load Stability |
Superior strength contributes to enhanced load stability |
Less stretch was applied to the pallets compared to cast film |
How to choose Stretch film for your cast or blown film needs?
The choice between cast and blown stretch wrap depends on the specific needs of the application. Cast stretch wrap is ideal for high-clarity and noise-sensitive environments. It is also quick and efficient for high-volume production.
Blown stretch wrap, on the other hand, is better suited for heavy-duty applications requiring high puncture resistance and load stability. Both types have their unique advantages and choosing the right one depends on the nature of the load, environmental conditions, and budget considerations.
Understanding the differences between cast stretch film and blown stretch film is crucial for selecting the right packaging material for your specific needs. The choice between these two types of film depends on factors like load weight, product shape, and production speed.
For high-performance stretch film for your industrial packaging needs, visit our website to explore our extensive selection. At Yuandian, We specialize in casting processing stretch film, with the state-of-the-art Nano technology to make cutting-edge power stretch film, with superior performance in many aspects compared with normal stretch film.As a trusted manufacturer, we offer wholesale and export services, ensuring access to the best packaging materials at reasonable prices.
To learn more about our superior performance stretch film products, please click it.
More News
2025-07-07
2025-07-14
2025-06-30
2025-06-23
2025-06-11
2025-05-30
2025-05-20
2025-05-10